Effective Risk Assessment (and the choice and implementation of controls) is based upon a good understanding of the work processes. This is used to set up procedures for determining what to monitor, who to monitor, when to monitor and what data to collect that is appropriate for the methods chosen.
When performing screening for MSD hazards, a preliminary risk assessment or a more comprehensive risk assessment, the Risk Assessment Team should talk first to workers, supervisors, managers and technical employees. This gives a necessary understanding of the work process and tasks.
Observing work tasks should be guided by: who, what, when, where and how.
Plan | Factors to Consider |
---|---|
Who? | Who to observe? The focus should be on hazards created by the work processes rather than on individual behaviours. Observe multiple people where possible. Perhaps observe tall and short persons at a minimum. An individual focus is relevant for incident investigation or Return to Work |
What? | What task or tasks to observe? Two main options:
|
When? | If tasks vary by day, week, product or service, a step of listing all tasks then performing a screening step to identify tasks/products/processes that may be most problematic is necessary. Observation or video recordings and risk assessment of only these selected tasks could then be performed, perhaps requiring multiple viewings. |
Where? | This may be dictated largely by the “when”, but some situations have particular challenges. For example, during toileting in a health care environment. |
How? | “How” is mainly driven by the input requirements of the risk assessment methods chosen.
|
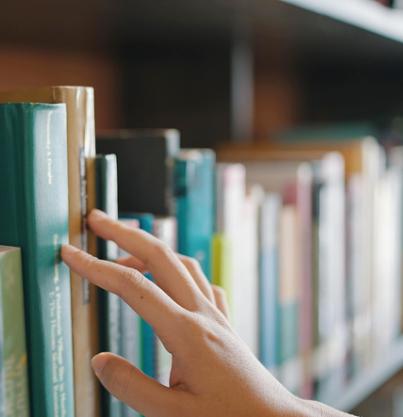
Want to search the resource library?
Find all the available resources on the MSD prevention website, including posters, videos, and links to relevant websites.