Is this the right version of the Guideline for your organization?
This BASIC version of the Guideline is intended for medium to large companies with an existing Health and Safety program who wish to improve their problem-solving approach to prevent MSD. This BASIC version is one part of the MSD Prevention Guideline.
The three versions of the Guideline use similar structure and language, so organizations may use any of the versions without having to change their approach if they wish to use another version.
Acknowledgements
The development of a New MSD Prevention Guideline for Ontario was a multi-stakeholder initiative led by the Centre of Research Expertise for the Prevention of Musculoskeletal Disorders (CRE-MSD) in consultation with representatives from the Ontario Health and Safety System, Ontario’s labour organizations, employer associations, and individual employers and workers. Their important contributions are gratefully acknowledged. The first edition of the Musculoskeletal Disorder (MSD) Prevention Guideline for Ontario is similarly acknowledged for providing materials that have been reused and modified in this Guideline.
Related Documents
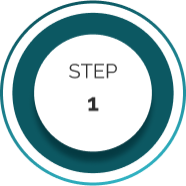
Demonstrate Management Commitment and Leadership
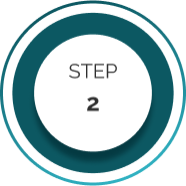
Facilitate and Encourage Workers’ Participation
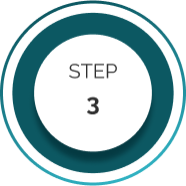
Plan Hazard Identification and Risk Assessment
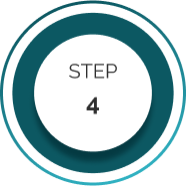
Conduct Hazard Identification and Risk Assessments
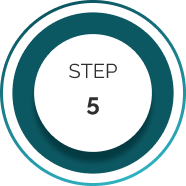
Develop a set of Targets and Goals to Eliminate Hazards & Control Risks
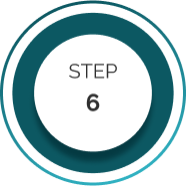
Control Hazards & Implement Changes to Achieve Targets & Goals
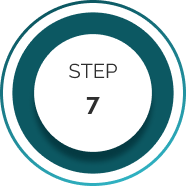
Provide Education and Training
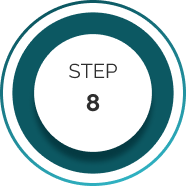
Evaluate Controls, the Program and the Organization’s Performance
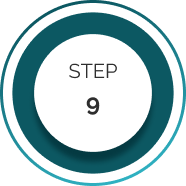
Document Lessons Learned and Stakeholders’ Feedback
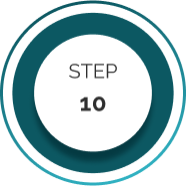
Review Processes, Achievements, and Identify Areas for Improvement
Basic Guideline (PDF)
Download the PDF version of the basic guideline here. The PDF version contains all the same information that is presented on the website.