MSD Prevention Guidelines
Select the appropriate Guideline
You may be a worker looking for information on low back pain or carpal tunnel syndrome or an organization looking to prevent musculoskeletal disorders.
We have created ways for different groups and people to get more quickly to content that is most useful to them.
Every organization is different and so the words “micro”, “small”, “medium” or “large” may not describe your organization well. To cater to the range of knowledge and resources in health and safety and ergonomics, we have created three parallel collections of resources for prevention of musculoskeletal disorders (MSD), Quick Start, Basic and Comprehensive Guidelines.
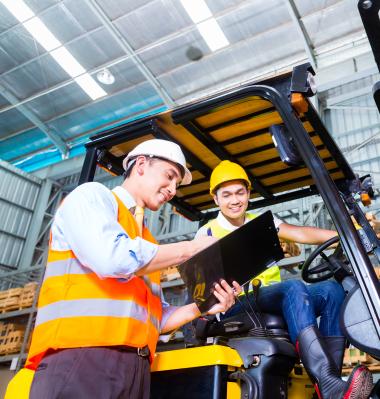
Comprehensive Guideline
The Comprehensive Guideline is best for organizations that:
• Have multiple persons and/or a Department with special knowledge, experience, and responsibility for Health and Safety
• Have a formal management framework that is used to oversee the organization's activities
• Are familiar with Occupational Health and Safety Management Systems such as ISO 45001 or CSA Z1000
• Have a formal or informal management system for Health and Safety
• Have comprehensive policies and procedures for health and safety that address most hazards but want to improve their MSD prevention activities.
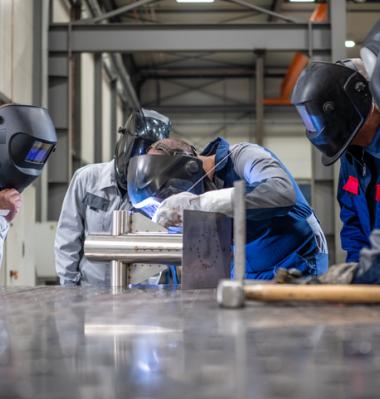
Basic Guideline
The Basic Guideline is best for organizations that:
• Have a Joint Health and Safety Committee (JHSC)
• Have a person or persons with knowledge, experience, and responsibility for Health and Safety
• Have policies and procedures for health and safety addressing most hazards but want to improve their MSD prevention activities
You may find that the Quick Start Guide or Comprehensive resources are also useful
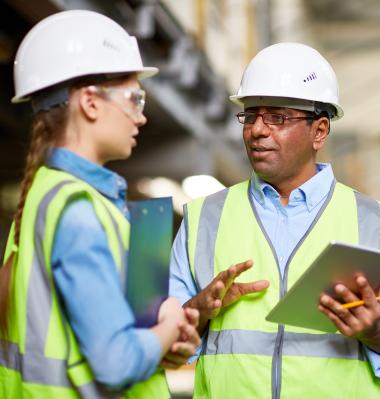
Quick Start Guide: General
The Quick Start Guideline is best for organizations that:
• Complete any type of work
• Are small or very small (also called “micro” businesses)
• May have a Health and Safety Representative
• May not have much knowledge and few resources in Health and Safety
• May be unfamiliar with MSD and their prevention
You may find that some of the Basic resources are also useful
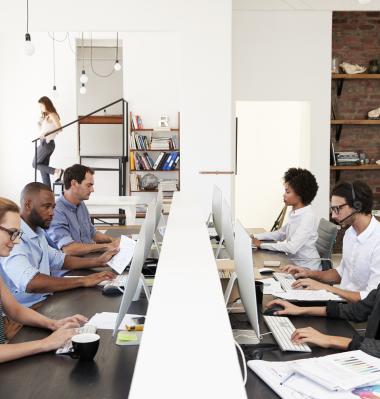
Quick Start Guide: Office
The Quick Start Guide: Office is best for organizations that:
• Complete computer-based work
• Are small or very small (also called “micro” businesses)
• May have a Health and Safety Representative
• May not have much knowledge and few resources in Health and Safety
• May be unfamiliar with MSD and their prevention
You may find that some of the Basic resources are also useful
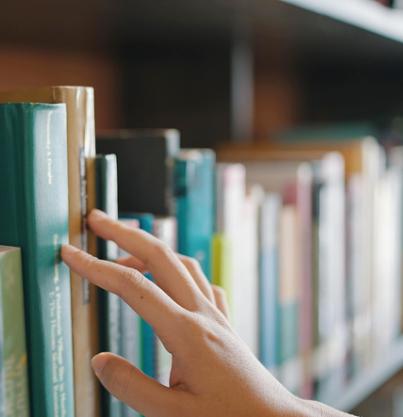
Want to search the resource library?
Find all the available resources on the MSD prevention website, including posters, videos, and links to relevant websites.